«Lean Production» als Produktionsmethode hat ihren Ursprung in der japanischen Automobilindustrie. Dort wurden lieferanten- oder kundenseitig bedingte Schwankungen bereits Ende der 80er Jahre anders aufgefangen, als zu dieser Zeit in den USA und Europa üblich. Heute hat das Konzept «Lean Production» einen fixen Platz in vielen Industrien und die Grundidee wurde auch in Methoden vieler weiterer betriebswirtschaftlicher Prozesse aufgenommen. Letztlich geht es darum, Prozesse zu automatisieren und ohne Unterbruch zu gestalten, sodass Kosten, Arbeitszeit und Material eingespart werden.
Stau oder umgekehrt saisonal bedingte Leere auf den Fertigungsinseln war gestern. Mit der Umstellung auf eine Fliessfertigung, bei der die Maschine kontinuierlich, ohne Unterbruch und Zwischenlager nach einer festen Taktzeit aufgebaut wird, kann die Durchlaufzeit pro Maschine deutlich reduziert werden. Mehr noch. Michael Schneider, Head Plant Switzerland, sagt dazu: «Die Steuerung der Produktion ist transparenter und die Planbarkeit effizienter geworden. Das sind riesengrosse Vorteile gegenüber der alten Methodik».
Beim Umbau der Produktionslinie konnte auf wertvolle Erfahrungen innerhalb der Aebi Schmidt Group zurückgegriffen werden. Denn auch die Kehrmaschinenproduktion in St. Blasien ist nach dem «Lean Production» System organisiert. Trotzdem mussten erst einmal alle Beteiligten für die Umstellung gewonnen und Zweifel ausgeräumt werden. Auf die Frage, ob denn die Mitarbeitenden heute zufrieden mit der neuen Produktionslinie sind, sagt Michael Schneider: «Die Arbeitsplätze wurden ergonomisch angepasst und die ganze Produktion ist nun aufgeräumter und heller, das gefällt schon. Zudem muss die Inbetriebnahme und Prüffahrt nun auch nicht mehr auf dem Vorhof des Produktionsgebäudes durchgeführt werden (das war im Winter nämlich nicht besonders beliebt), sondern es gibt nun neu einen integrierten, stationären Prüfstand, wo jede Maschine ganz genau kontrolliert und parametriert wird.»
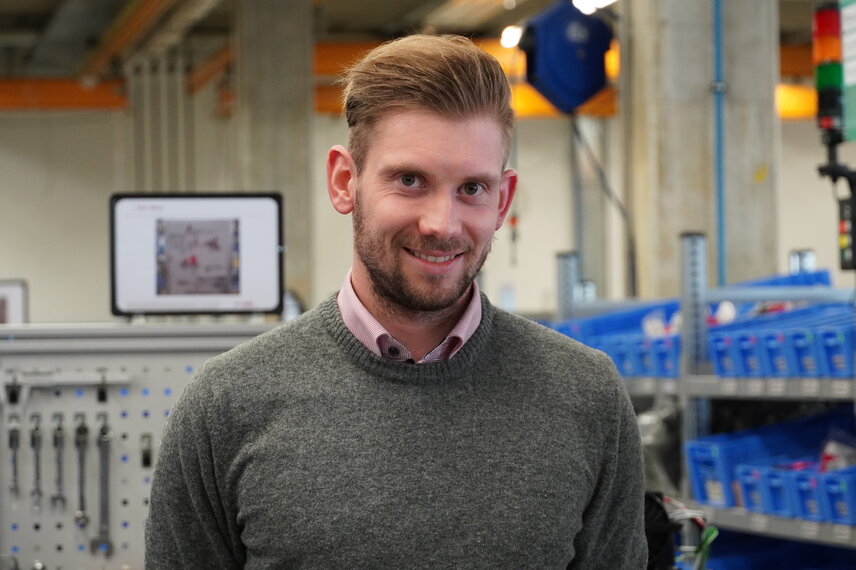
Auch das selbststeuernde Kanban-System auf der Linie begünstigt eine ressourcenschonende Materialversorgung. «Wir können nun den kontinuierlichen Verbesserungsprozess viel besser als vorher gewährleisten. Auf Schwankungen bei der Nachfrage können wir sofort und vor allem mit allen Mitarbeitenden reagieren – das war früher weitaus komplizierter. Die flexible Auslastung funktioniert gut und im Vergleich zu vorher können mit der neuen Methodik bei Bedarf an einem Tag doppelt so viele Maschinen wie vorher produziert werden,» sagt Schneider stolz.