Schmidt |Spreader|Galeox NT
Concept
The Galeox NT is very stable as the base frame and tail section are integrated into the hopper and it uses proven Stratos components as its basis. The steel hopper is blasted and powder coated for greater corrosion protection. The spreader also has a corrosion-protected, water-tight aggregate compartment.
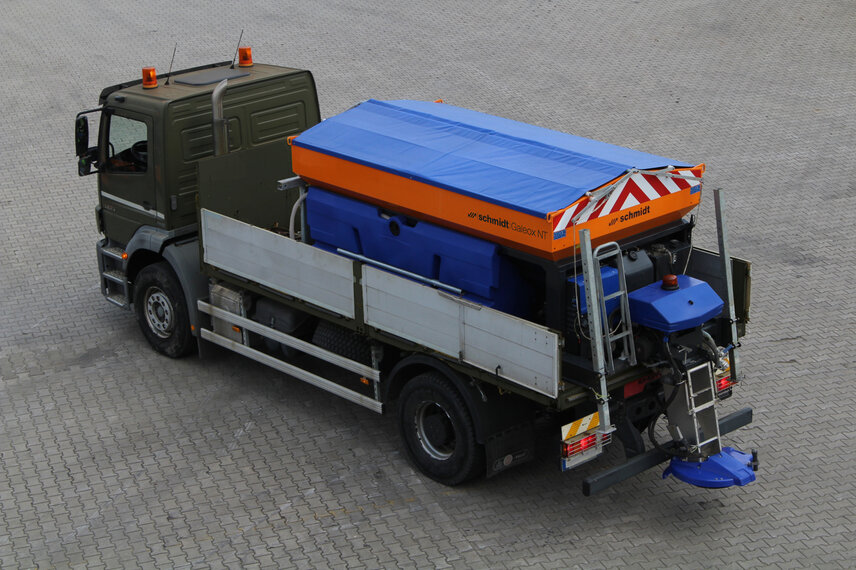
Mounting and demounting systems
Each of the spreaders can be equipped with one of two mounting and demounting systems:
- Base frame for demounting legs, tipper system or fixed mounting
- RoRo (roll on - roll off) system
Both variants can be demounted with an empty hopper and full brine tanks.
Dosage and conveyor system
The belt conveyor system ensures a constant feed rate. This ensures high dosing accuracy, irrespective of the spreading material’s moisture content. The precise dosage of all commercially available spreading materials is enabled by the accurately adjustable belt speed as well as a feed gate. The feed gate is equipped with an integrated lump-crushing function to ensure a flawless spreading operation.The integrated V-shaped, endlessly-profiled conveyor beltensures even transportation of the spreading material, while a stainless steel guide plate makes it possible for the belt to glide at full surface contact and minimum friction. The drive roller is mounted on low-maintenance bearings.
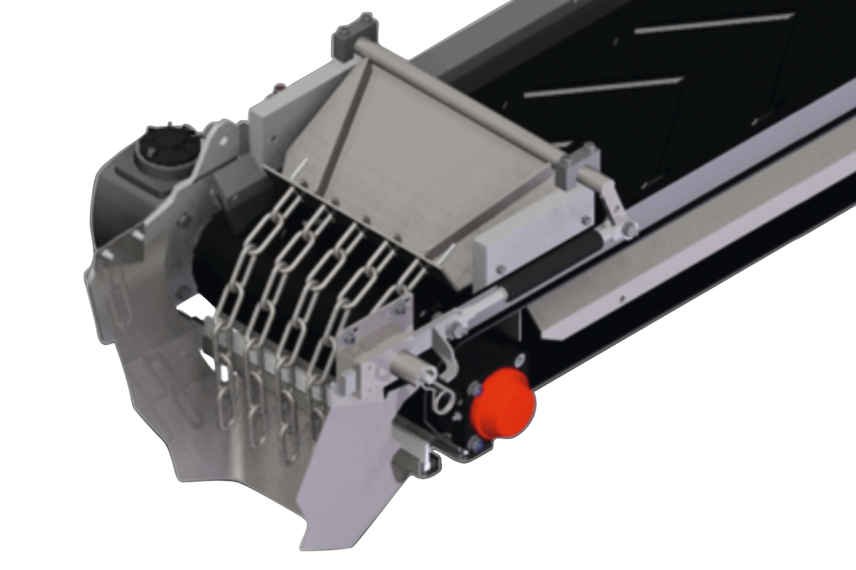
Pre-wet equipment
The spreader can be equipped with lateral brine tanks with a liquid level indicator, integral brine tank ventilation and a brine pump with run-dry protection. The size of the pre-wet tanks is approximately 30% of the hopper volume. A rear-side Storz C connection is available for filling and emptying the brine tanks. When switching on the brine (FS 30), the dry material is automatically reduced and the distribution system settings are optimised in accordance with the change in composition of the de-icing agent. The system achieves a high level of accuracy, thanks to integrated sensors for comparison of the actual versus the target value of the control loops.
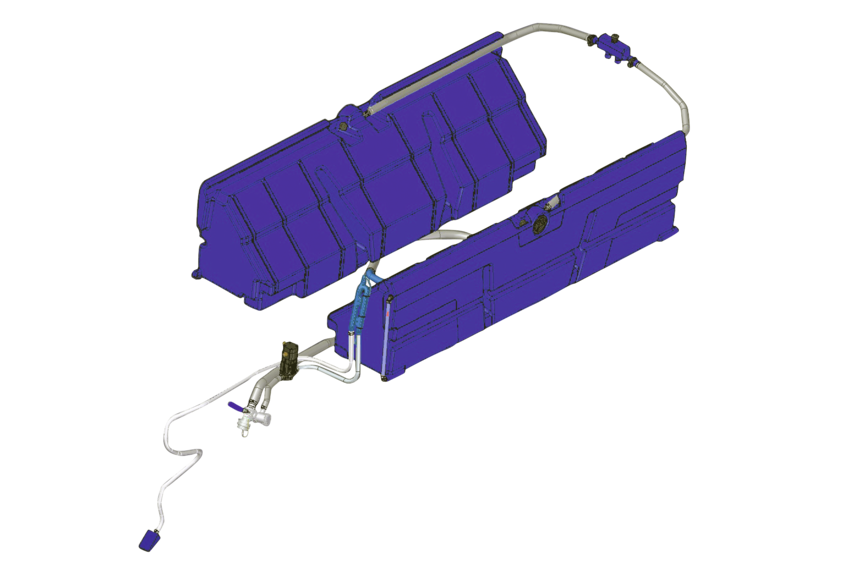
Distribution system
The distribution system is made completely of stainless steel and can be folded using gas pressure springs. The spreader has an open stainless steel chute with height adjustment to allow a smooth material flow. An asymmetrical spreading pattern adjustment is achieved by swivelling the lower end of the chute while a mixing system ensures homogeneous mixing. A 490mm diameter spreading disc is used, which allows economical use of spreading material, while the spreading width depends on material and circumstances.
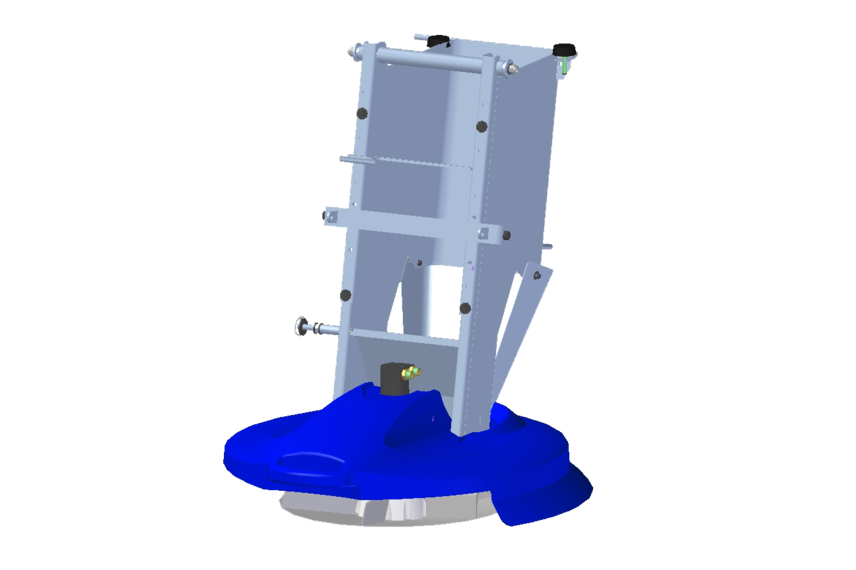
Drive options
There is also a choice of drive systems. The Stratos spreaders can be ordered with vehicle hydraulics, rotopower or diesel engine.
- Vehicle hydraulics: The spreader is simply driven by the hydraulic system of the carrier vehicle.
- Rotopower: The required drive power is taken directly from the rear wheel hub and used for the drive.
- Motor drive: The diesel engine is integrated into the rear of the spreader, which means that no additional build up length required.
Control and information systems
A digital, fully road-speed related EC or EP control system is used, which makes work easier and more efficient. The control unit has easy-grip click-turn knobs and illuminated push buttons - all parts are waterproof and highly resistant. The simple menu structure allows the control unit to be quickly adapted to the application conditions.
Options
- Rotating beacon (LED)
- Red and white marking
- Winter service marking
- Splash guard 2,000 or 2,200mm
- IntelliOPS