On behalf of the Ministry of Infrastructure and Water Management, Rijkswaterstaat manages and develops the main roads in the Netherlands and is thus also responsible for de-icing. Already since 2018, all new spreading vehicles from Rijkswaterstaat are equipped as standard with a Route Assistant, a part of the system where the driver is guided along a predefined route with GPS support and the gritting settings are made fully automatically. The driver can concentrate on driving. The Route Manager system optimises the routes.
"Thanks to the route manager, I use about 20 to 25% less salt per route," says Harold van Os, winter maintenance coordinator at Rijkswaterstaat and the main person responsible for introducing the Route Manager. To achieve this, Harold van Os initially focused on a small number of spreading vehicles and routes. "When the results of the first test vehicles and routes were positive, I was tasked with rolling out the systems across the entire Netherlands as soon as possible."
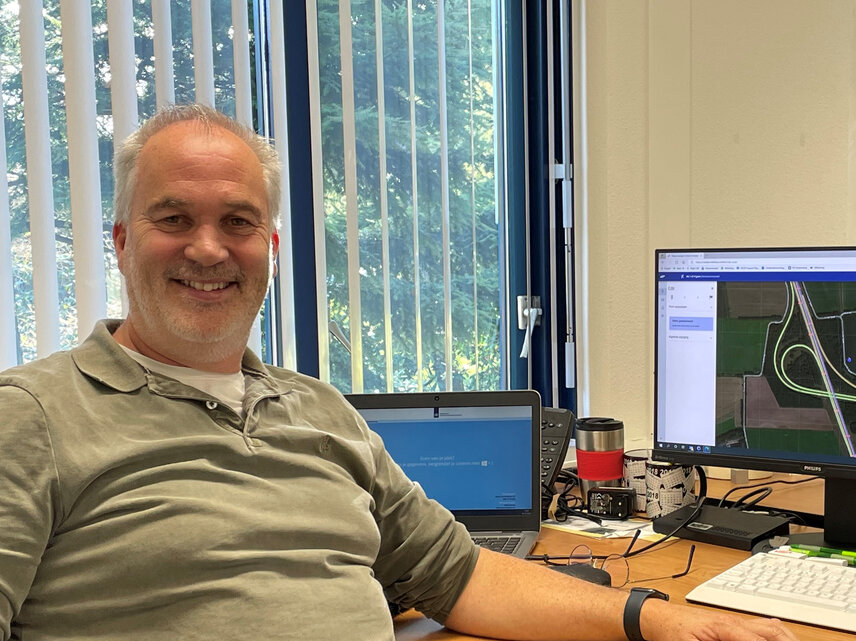
We drive the routes in spring and summer with a car and a suitcase with the route recording devices. Then I import and optimise the driven routes in the Route Manager. Finally, we load the routes back into the control panel, the Route Assistant, and I ask the driver for feedback. The faster we implement the drivers' feedback, the faster we achieve the desired savings," explains Harold van Os. "The driver is and remains the specialist on his routes and he actively contributes to improving the process. In the end, you usually see that the drivers are also really proud of the results of the optimised routes."
During the preparation period and test phase of the system, Harold van Os worked closely with Aebi Schmidt to optimise the routes for Den Bosch, a motorway section combined with a provincial and municipal road, as well as feeder roads and emergency exits. "Den Bosch was the perfect case study for us because all kinds of situations could be found there," explains Harold van Os. "We also deliberately wanted to include Aebi Schmidt's broad experience in the test phase. If, for example, a function was missing in the Route Manager, I could report it back to Aebi Schmidt, whereupon it was taken into account accordingly in the next software update. Den Bosch is now our benchmark. Our regional advisors now get access to the system and we train them per region so they can work on their routes independently."
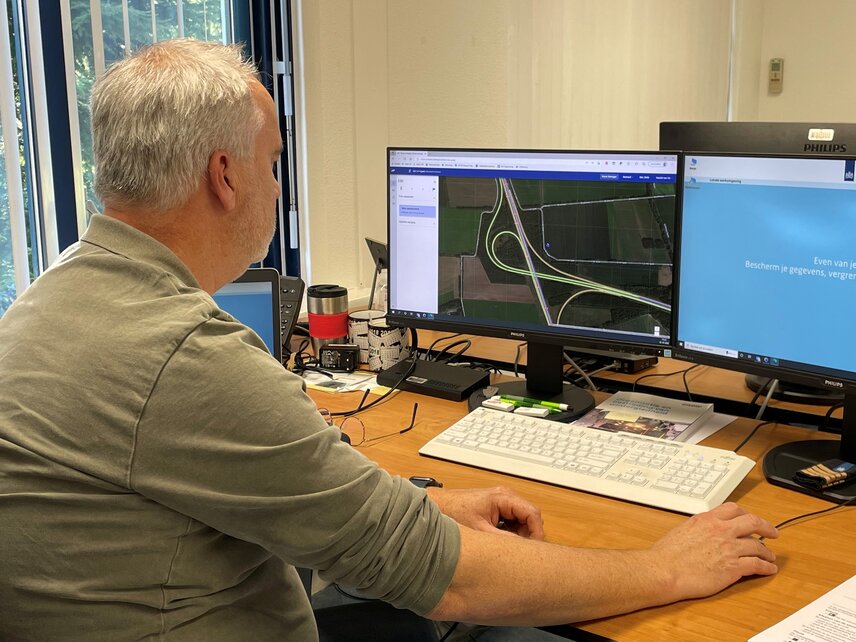
Rijkswaterstaat faces several challenges. "We can only spend our money once and we want to use our resources as efficiently as possible, but the safety of road users and spreading vehicle drivers must not be compromised. The route manager helps us to save salt, resources and thus money. At the same time, the system contributes significantly to a perfectly gritted route and thus increases safety," says Harold van Os. "In addition, although we have our own spreading vehicles and snow ploughs, the operations are carried out by contracted third parties. The Route Assistant makes it easier to deploy drivers on different routes, including those they know little or nothing about. We see that the contractors also appreciate this very much.“
When asked about his most important advice for other clients, Harold van Os answers: "Start with the most complex route. You learn the most from that and create a benchmark that you can use for other routes. At the beginning it takes a little longer, but in the meantime I only need about one to one and a half hours until I have optimised a route. In the end, very little effort, for an optimal spread and a big gain for safety."
Would you like to know more about Route Manager? The following video gives you more insight.