La «lean production», en tant que méthode de production, puise son origine dans l’industrie automobile japonaise. Dès la fin des années 80, les fluctuations liées aux fournisseurs ou aux clients furent gérées différemment de ce qui se faisait à l’époque aux États-Unis et en Europe. Aujourd’hui, le concept de «lean production» a trouvé sa place dans de nombreuses industries et l’idée de base a également été reprise dans les méthodes de nombreux autres processus de gestion d’entreprise. Il s’agit en fin de compte d’automatiser les processus et de les organiser sans interruption pour économiser des coûts, du temps de travail et du matériel.
Les engorgements ou, à l’inverse, les périodes creuses saisonnières sur les îlots de production, sont révolus. Grâce au passage à une production en flux continu, qui permet d’assembler la machine en continu, sans interruption ni stockage intermédiaire, selon un temps de cycle fixe, le temps de passage par machine est considérablement réduit. Et bien plus encore. Michael Schneider, Head Plant Switzerland, ajoute: «Le contrôle de la production est devenu plus transparent et la planification plus efficace. Ce sont des avantages immenses par rapport à l’ancienne méthode».
Lors de la transformation de la ligne de production, les expériences acquises au sein du groupe Aebi Schmidt ont été une aide précieuse. En effet, la production de balayeuses à Saint-Blaise est aussi organisée selon le système de «lean production». Cependant, il a d’abord fallu convaincre toutes les personnes concernées par le changement et dissiper les doutes. Quand on lui demande si les collaborateurs sont aujourd’hui satisfaits de la nouvelle ligne de production, Michael Schneider répond: «Les postes de travail ont été adaptés sur le plan ergonomique et l’ensemble de la production est maintenant plus ordonné et plus clair, ce qui est appréciable. De plus, la mise en service et les essais ne doivent plus être effectués sur le parvis du bâtiment de production (ce qui n’était en effet pas très apprécié en hiver), mais il y a désormais un banc d’essai fixe intégré permettant de contrôler et paramétrer très précisément chaque machine.»
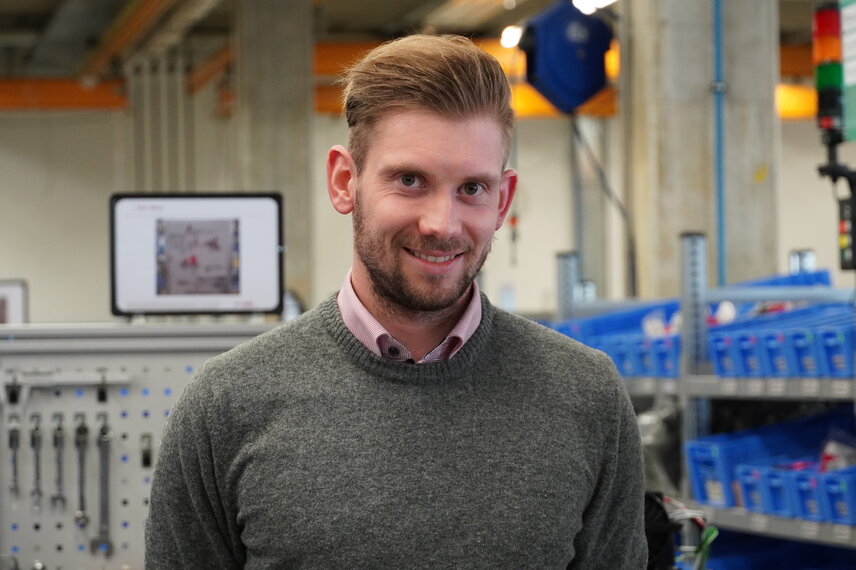
Le système kanban autoguidé sur la ligne favorise également un approvisionnement en matériaux économe en ressources. «Nous pouvons désormais garantir le processus d’amélioration continu bien mieux qu’auparavant. Nous réagissons immédiatement aux fluctuations de la demande et surtout avec tous les collaborateurs, ce qui était bien plus compliqué auparavant. La répartition flexible de la charge de travail fonctionne bien et, par rapport à avant, la nouvelle méthodologie permet, si nécessaire, de produire en un jour deux fois plus de machines qu’auparavant», déclare fièrement Schneider.