Schmidt |Sweeper|AS 990 / ASC 990
Cleaning concept
The Schmidt AS 990 / ASC 990 delivers perfect sweeping results with a large area coverage and at the same time ensures safe traffic routes on the entire airport site. Thanks to the permanent magnet bar, two disc brushes, the blast nozzles mounted on both sides and the rear-mounted suction unit, the machine cleans large areas comprehensively and quickly in a single pass. Objects of various types and origins (FOD, metals, dirt, leaves, etc.) are reliably removed. With the optional and quickly exchangeable liquid suction unit, the AS 990 / ASC 990 offers a complete solution.
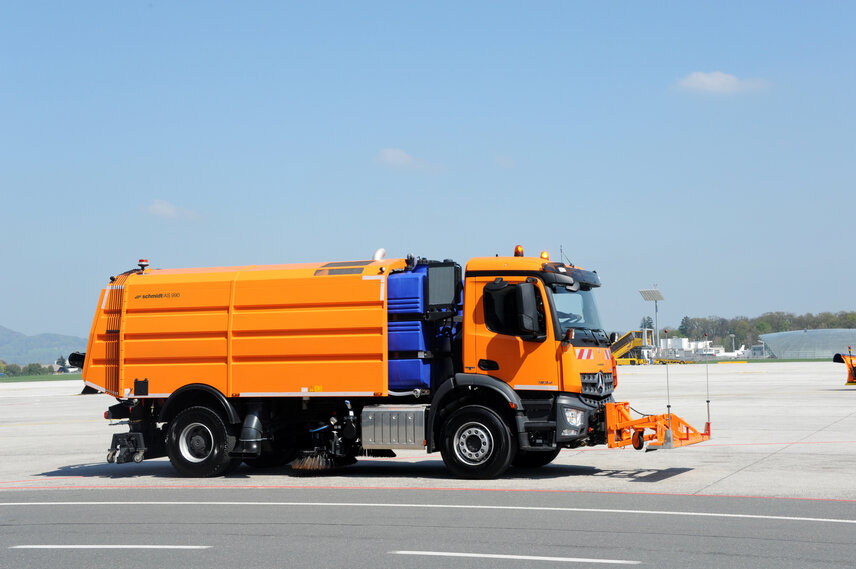
Permanent magnetic bar
The removal of foreign object debris (FOD) at an airport has a major impact on the safety and efficiency of flight operations. Therefore, the recommended Schmidt PMB 2400 permanent magnetic bar is an indispensable tool for removing magnetic, particularly dangerous foreign objects from stands, taxiways and runways. The PMB 2400 can be attached to the pre-assembled front mounting plate in a simple operation.
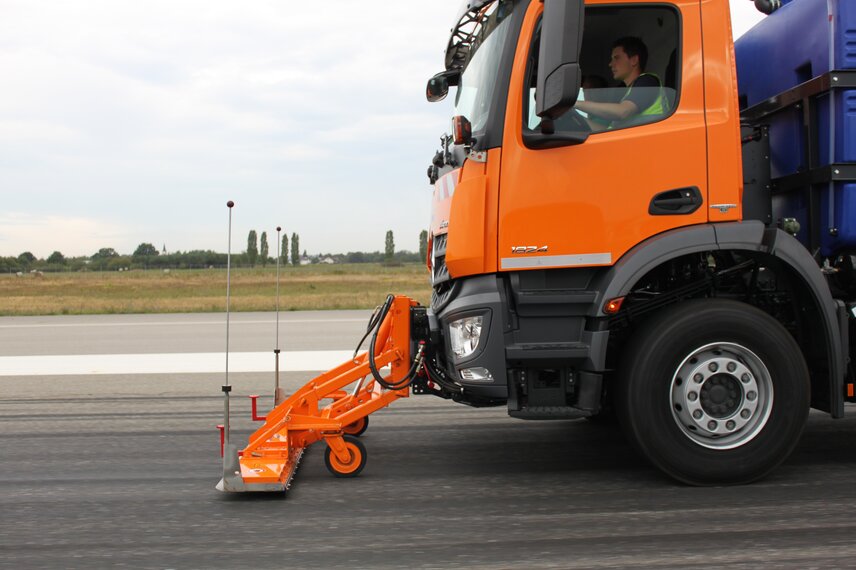
Disc brushes
The two optional disc brushes enable an increase in sweeping width and a more comprehensive cleaning. Both ground contact pressure as well as swivelling pressure can be pneumatically adjusted and optimally adapted to the specific operating conditions. The integrated water spray nozzles ensure effective dust control, guaranteeing safe and clean working conditions.
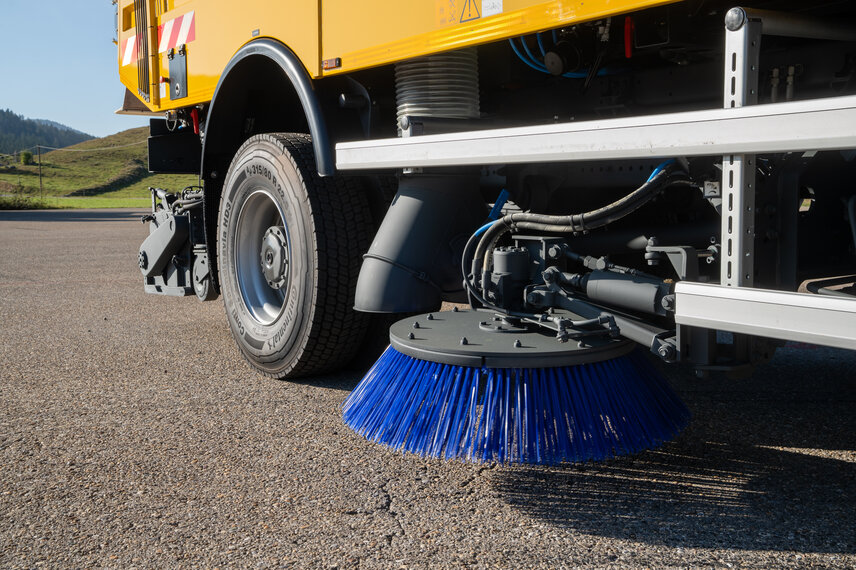
High-performance suction fan
The power of the high-performance suction fan can optimally be adapted to the amount of dirt. A speed sensor is built into the hydraulic, which monitors the speed / performance of the suction fan. Stepless adjustment is also possible. The speed is controlled hydraulically and can be adjusted via the control panel. The high-performance suction fan supplies the lateral blast nozzles with air flow as well as the rear suction unit and the optional manual suction hose with suction air. Compared to a conventional V-belt or toothed belt drive, the suction blower requires no maintenance. The impeller and the housing are made of high-wear-resistant metal.
Blast nozzles
The optional blast nozzles achieve a high performance across the entire working width as well as alongside the truck. This ensures an optimum cleaning of the airport area. The blast nozzles are available with pneumatic height adjustment and with that guarantee an even better cleaning result in every situation.
Suction and sweeping system
The rear suction unit has two suction ducts (width: 2 x 1,150 mm), which are airflow-optimised and coated on the inside with a hot-vulcanised wear protection as a standard. This ensures less friction and less wear. The rear suction unit has a symmetrical weight distribution for optimised sweeping results. The sweeping pattern can also be adjusted continuously from the outside and features a wear indicator with colour scale.
Roller brush
In addition to the two suction ducts, a sweeping roller is used for faster sweeping (mechanical sweeping). This extends across the entire working width and is automatically raised when obstacles are encountered. Sweeping speeds of up to 40 km/h are possible.
Integrated debris flap
In the standard version, a debris flap is integrated into the rear suction unit. It works pneumatically and can be operated from the driver's cab. As a result, larger debris can be picked up. An optional liquid flap for improved collection of liquids can be configured as an option.
Exhaust air diffuser
The two suction ducts suck the air containing debris into the hopper. Debris is separated in the hopper by gravity. The exhaust air is discharged upwards over the hopper. A diffuser can be installed in the roof to regulate the air flow. For easier cleaning, it can be swivelled pneumatically.
Liquid suction unit
The liquid suction unit is specially designed for collecting liquids such as water or de-icing agents (for example optimum glycol absorption of 96 to 99%). It comes with two suction ducts (width: 2 x 1,250 mm), which have an airflow-optimised design and are coated on the inside with a hot-vulcanised wear protection coating as a standard. This ensures lower friction and less wear. The liquid suction unit can be fitted individually or in combination with the rear suction unit.
Suction unit attachment system
The rear suction unit (A) and the liquid suction unit (B) can be installed individually at the rear, whereby the liquid suction unit can also be installed between the axles individually (C) or in combination (D) with the rear suction unit. The suction units are attached via a flexible lifting device that is independent of the chassis. This enables optimum ground adaptation during operation. The running wheels with integrated return mechanism guide the suction units reliably over the road surface. The optional quick-change system from Aebi Schmidt allows the rear suction unit to be exchanged for the liquid suction unit without tools in just a few minutes (A+B).
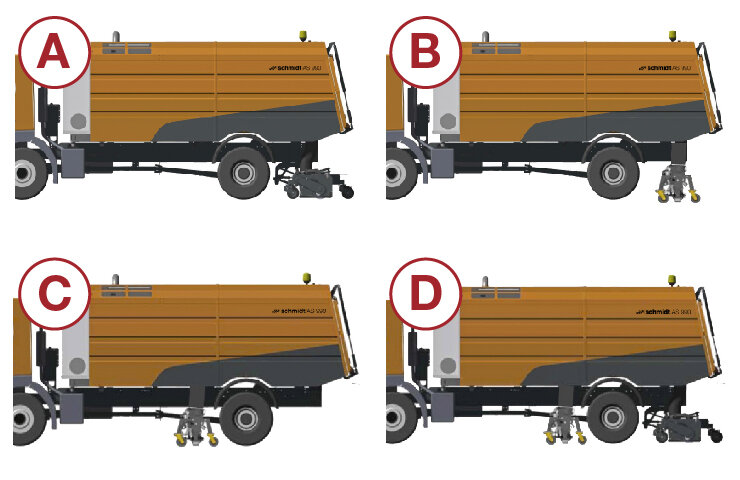
Hopper
The generously dimensioned hopper has a capacity of 9.5 m³ and is equipped for large quantities of debris. As standard, the hopper floor is made of stainless steel. The hopper can be tilted hydraulically and offers safe emptying thanks to the 52° tilting angle. The hopper can be tilted without starting the auxiliary engine and is operated via a separate remote control, which is stored in a watertight storage box.
Water tank
The corrosion-resistant water tank is installed between the cab and the auxiliary engine to reduce noise and has an easily accessible cleaning opening. It has a capacity of 2,000 l and is made of polyethylene (PE). The associated water pump with a maximum pressure of 10 bar at 37 l/min is hydraulically driven and safe to run dry. Water spray nozzles are mounted in front of the suction unit, in the suction duct and suction pipe as well as on the optional disc brushes for optimum dust control. The winter function offers optimum protection thanks to automated blow-out of the entire water system (frost protection function). An supplementary water tank with an additional 2,000 l can be added as an option.
Configuration possibilities
The equipment recommended by Aebi Schmidt experts includes the permanent magnet bar, the disc brushes and two blast nozzles. In addition, we recommend the rear suction unit with the optional quick-change system for the liquid suction unit, which is particularly characterised by its flexibility and maintenance-optimised design. The concluding feature is the exhaust air diffuser installed in the hopper, which is engineered for a secure work process. We also offer the following configuration options as series standard:
Extended options
- Manual suction hose
A manual suction hose can be mounted on the rear door of the hopper for cleaning work in gullies, water shafts, etc. The hose diameter is 200 mm and the control unit is attached directly to the manual suction hose. - Hose reel with cleaning hose
This enables rough cleaning of the hopper or the sweeper after emptying. The water hose is 10 metres long and has an adjustable water spray nozzle. Water is supplied via the hydraulically driven water pump. - Leaf screen cleaning unit in the hopper
The leaf screen cleaning unit makes it easier to clean the hopper. A water spray nozzle pipe with water spray nozzles enable simple and optimised cleaning of the leaf screen and the area above the leaf screen. - Water outlets on the rear hopper door
In order to be able to drain excess water or de-icing liquid if necessary (e.g. before the hopper is completely emptied), a water drainage outlet is mounted on the rear door of the hopper. - Rear area monitoring
A camera is mounted on the hopper door. It is switched on automatically as soon as reverse gear is engaged. The image is shown on the display of the control unit. - Extendable side suction ducts
In addition to the suction units, two suction ducts can be fitted on the left and right in front of the rear axle. This increases the suction width by 500 mm in each case. The suction ducts are pneumatically operated and have a lateral adjustment range of 320 mm. Suction is possible when the suction duct is extended or retracted to the side. The integrated water spray nozzles also ensure optimum dust control.
Special version: Schmidt ASC 990
By applying a detergent and water mixture, the Schmidt ASC 990 also cleans aircraft stands. The soiled area is damped with the cleaning emulsion using the additional spray bar in front of the disc brushes. The surface is then treated and roughened with the disc brushes. The loosened material is collected in the hopper via the rear suction unit. This version is particularly suitable for intensive cleaning of traffic areas.
High-pressure cleaning equipment using rotary spray nozzles
An efficient high-pressure cleaning bar, which operates at up to 200 bar and 70 l/min, can also be mounted in front of the liquid suction unit. This enables cleaning over a width of approx. 2,400 mm while simultaneously extracting water and dirt completely. This option enhances the results delivered even further.